Aspire Tower
Stunning façade design with DOGLA-TRIO
The 318-meter Aspire Tower is the design landmark of the Asian Games 2006 in Doha, Qatar. Located directly next to the Games' stadia, construction of the large, torch-shaped tower commenced in April 2005.
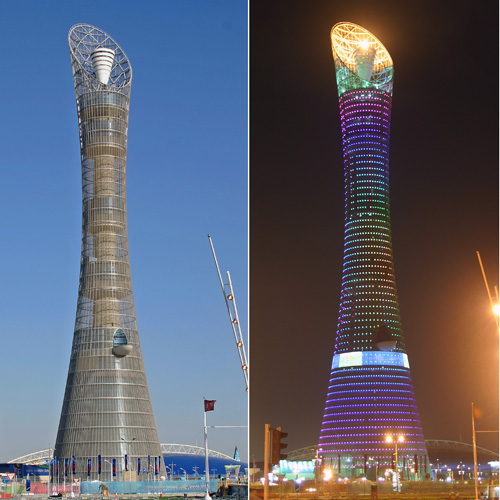
Gallery
Description
The façade consists of 3452 single elements with a total area of approximately 30,000 square meters.
LEDs have been installed throughout the façade to create user-defined effects in varying colours.
The Architectural Mesh Façade
At the bottom, the Aspire Tower has a diameter of approximately 70 meters. Towards the center it reduces to approximately 27 meters. The maximum diameter at the top measures around 45 meters. The construction time of the tower was just 15 months, excluding interior finishings.
The architectural brief was to create a similar transparency in each part of the tower from one viewing point. This was achieved by increasing the opening progressively from bottom to top. By using different opening sizes, the transparency can be adjusted to construction conditions, accounting for different viewing distances and perspectives. Even with extreme angles such as 5 degree (looking up from the bottom), the larger open area in the top part of the tower still offers transparency in the mesh. Different viewing angles let the mesh appear similarly open over the full height creating a homogenous façade.
Using the mesh type DOGLA-TRIO, it was possible to vary the clear openings of the horizontal wires between 14 and 44 mm. The open area was incrementally increased from 72% to 85%.
The vertical wire groups of DOGLA-TRIO consist of three specially preformed wires. W.S. Tyler ensured that these wire groups run in one continuous line from element to element across the full height of the tower. The standard elements are 8 meters high with a maximum width of 1.96 meters. Special elements are as long as 13 meters.
Utilizing the trapezoidal form for all elements, the wire mesh can clad circular buildings of varying diameters such as the Aspire Tower. The polygonal layout makes the façade appear circular without the requirement for costly panel form bending.
The Mounting Solution
The mounting system was developed by Haver & Boecker and coordinated with the façade planners and metal contractors. At the top, each mesh element is equipped with an open-hook strip, which is inserted into a bespoke L-Profile attached to the framework. The bottom part of the panel has a flat tension profile with clevis screws and pressure springs at approximately 200 mm centers, which allow for individual tensioning of each element. To reduce deflection and inherent vertical loadings, each element is connected in the center to round tubes behind the mesh using wire connectors.
W.S. Tyler supplied ready-to-install mesh panels direct to site, where they were tensioned into frames in a specially built manufacturing hall. As a final step, the frames were lifted to their final destination on the façade, where they were connected to the structure of the tower.
Due to the tower’s height and exposed location, extreme standards for noise emission and windloads were required. The effectiveness of wire mesh for such projects was proven by means of various tests in a wind tunnel.